<< назад : вперед >>
Проблемы
развития метизного производства для автомобильной промышленности России
Необходимость
повышения качества и технического уровня крепежных деталей и пружин для обеспечения
потребностей автомобильной промышленности сегодня ни у кого не вызывает сомнений.
На
автомобильных заводах понимают, что повышение конкурентоспособности
российских автомобилей и их качества, которого ждут все нынешние и
потенциальные автовладельцы, зависит (в том числе) от качества крепежа и
пружин…
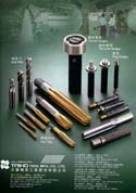
подробнее
Перспективы
внедрения прогрессивного крепежа в автомобильной промышленности России
В
настоящее время на сборочных линиях и в цехах Волжского автомобильного завода
используется крепеж, разработанный и изготовленный по нормативной
документации, переданной с технологией FIAT–ВАЗ в середине 60-х годов
прошлого столетия…
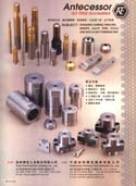
подробнее
Прогрессивный крепеж
– источник снижения затрат на производство и эксплуатацию АТС
Покупая
автомобиль, обычно принимают во внимание соотношение его качества и цены, не
упуская из внимания системы безопасности, длительность пробега без
регулировок и ремонта, эксплуатационные расходы. При этом едва ли кого-нибудь
интересует, какие крепежные детали использованы в сборке автомобиля…
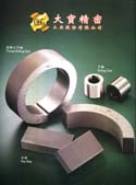
подробнее
Технический контроль
качества автонормалей у производителя, дилера и потребителя
Основная
прибыль от продажи автомобильных и автомоторных крепежных деталей зависит от
объемов спроса, заявленной цены, рекламы, ассортимента и товарного качества
продукции…

подробнее
Разделительные операции в
технологии холодной объемной штамповки деталей
Технология
изготовления деталей холодной объемной штамповкой строится на основе
необходимого и достаточного количества…
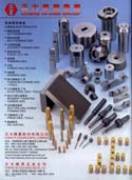
подробнее
|
Винтик, шпунтик и гаечка
Игорь
Моржаретто
Базар на
окраине, где торговали дефицитными запчастями для «жигулей», остался в
прошлом. Рынок автокомпонентов в России превратился в мощную индустрию; ее
оборот в этом году – 17 млрд. долларов. Состояние дел в отрасли анализируют
Игорь Моржаретто и Сергей Целиков.
ЦЕНА ДЕТАЛИ
Сразу определимся с терминами, поскольку рынок автомобильных компонентов
подразделяется на первичный (компоненты, которые используются для
производства автомобилей на конвейере) и вторичный (запчасти для продажи через
сервис и магазины). В мировой практике соотношение между ними примерно 70:30.
В России – свои традиции, оттого структура рынка автокомпонентов изрядно
смещена в сторону «вторички»: как 40 к 60. Причин тому несколько.
Во-первых, наш автопарк откровенно старый и требует постоянного обслуживания
и ремонта. Доля легковых автомобилей старше 10 лет в нем превышает 50%, а на
относительно беспроблемные в возрасте до 5 лет приходится всего чуть более
20%. Причем эксплуатируется очень много устаревших отечественных моделей.
Например, вазовская «классика» составляет 28,4% всех легковых машин, разные
«москвичи» – 6,6%, «волги» – 6%, «запорожцы» – 3,3%, «уазики» – 2,5%.
Во-вторых, дороги у нас по качеству весьма далеки от европейских. В-третьих,
по числу аварий на тысячу автомобилей Россия – на одном из первых мест в
мире. Даже по официальным данным раз в год в аварию попадает каждый сто
пятидесятый автомобиль, но в реальной жизни это число как минимум в три раза
выше.
Оборот российского рынка компонентов для легковых машин сопоставим с оборотом
самого рынка автомобилей. В 2007 году объем первичного рынка составит 7–8
млрд. долл. (примерно половину комплектующих произведут непосредственно на
автозаводах).
При этом 90% комплектующих предназначено для традиционных российских
автозаводов. Тем не менее локализация сборки иномарок хоть и медленно, но все
же идет. По нашим оценкам, к 2010 году доля компонентов для новых сборочных
производств вырастет до 30–35%. А объем первичного рынка увеличится до 15
млрд. долл.
Объем вторичного рынка автокомпонентов и запчастей по итогам 2007 года
составит 10–12 млрд. долл. Оценивая рост парка и изменение его структуры,
можно предположить, что к 2010 году он вырастет до 13–15 млрд. долл. и
сравняется с первичным.
К наиболее крупным сегментам рынка можно отнести шины (2,2 – 2,4 млрд. долл.;
подробнее – ЗР, 2007, № 7), масла (1,1–1,2 млрд. долл., ЗР, 2006, № 12),
аккумуляторы (500–600 млн. долл., ЗР, 2007, № 10), фильтры (250–300 млн.
долл.).
На рынке автокомпонентов сейчас насчитывается до двух тысяч игроков разного
масштаба. Лидирующие позиции пока занимают отечественные заводы. Тем не менее
активно идет процесс вытеснения российских брендов высококачественной
продукцией из Европы, а также более дешевыми запчастями из Китая, Турции и
Индии.
ВСЕ ТЕЧЕТ, ВСЕ МЕНЯЕТСЯ…
Концепция развития автомобильной промышленности, принятая правительством РФ в
2002 году, свою задачу выполнила: в страну пошли инвестиции. Сейчас уже
работают (или строятся) семь новых сборочных предприятий, еще ряд проектов – на
этапах всяческих согласований. Доля иномарок в легковом автопроме по итогам
2006 года составляла 23,6%. По нашему прогнозу, к 2010 году она должна
увеличиться до 60–63%. К тому моменту сборочные предприятия «разгонятся» до
1–1,2 млн. иномарок в год; выпуск «старых» марок будет снижаться.
Это заставляет мировых производителей автокомпонентов задуматься о
собственных предприятиях в России. Аналитики ожидали активного прихода
иностранных компаний уже в 2007 году. Но хотя «в продолжение» 166-го
постановления в прошлом году принято 566-е постановление правительства, по
которому и производители компонентов могут получить льготный режим
промсборки, говорить о бурном развитии российской отрасли «новой формации»
пока не приходится.
Министерством экономического развития и торговли уже подписано четыре новых
соглашения о производстве компонентов: с КамАЗом (там создано два СП – с
компаниями ZF и Cummins), ярославским заводом «Автодизель», а также с Toyota
Boshoku (подразделение «Тойоты»). Кроме этого, как рассказал исполнительный
директор Национальной ассоциации производителей автомобильных компонентов
Михаил Блохин, есть еще 30 проектов, претендующих на промсборку.
К нам хотели бы прийти европейская компания Auto- motive Lightning (фары,
фонари и т.д.) и американская Lear (жгуты электропроводки). Фирма TiRad из
Японии решила построить в Нижнем Новгороде завод радиаторов; о выходе на
российский рынок думают также подразделение корейской компании «Хёндай»,
английская Stadco. Крупнейший мировой производитель компонентов – канадская
Magna International собирается вложить более 30 млн. долларов в строительство
собственного завода в Татарстане, а также открыть два СП – с АВТОВАЗом и
ГАЗом. Но, по словам М. Блохина, процедура оформления льгот пока не
проработана и это серьезно затрудняет процесс.
Не стоит забывать, что в России уже выпускают немалую часть комплектующих
(см. Нашу справку), многие марки находятся в стадии организации производства
либо проработки технических вопросов. В целом с участием иностранного
капитала на территории России работает несколько десятков компаний –
производителей автомобильных компонентов и запчастей.
ПОБЕДИТ ДРУЖБА
Во всем автомобильном мире давно идет процесс консолидации. Выгоды налицо, в
первую очередь – сокращение затрат на всех этапах производства, от разработки
до продвижения конечной продукции. В мировом масштабе за последнее
десятилетие произошли уже сотни слияний и поглощений компаний. На российском
рынке производители компонентов традиционно группировались вокруг АВТОВАЗа,
который выпускал более 70% легковых автомобилей в стране. Самым крупным стал
дивизион «Автокомпоненты» группы компаний «СОК». В него входит 11 предприятий
в разных городах России (в собственности группы), еще пять сторонних заводов
находятся в управлении. В «СОК» также входят «Иж-Авто», ВИС и «РосЛада».
Другая самарская группа – «Автоком» объединяет восемь предприятий по выпуску
автомобильных компонентов и запчастей; в нее также входит Серпуховский
автозавод (СеАЗ).
Консолидация пошла и в шинной отрасли. За последнее время в России
образовалось два крупных холдинга – «Амтел» и «Сибур». В первый входит шесть
предприятий шинной индустрии, во второй – четыре достаточно крупных шинных
завода. Начался процесс объединения и среди производителей аккумуляторов.
Все это отрадно, но в мировой автомобильной индустрии идет и другой процесс –
унификации узлов, агрегатов и даже платформ; одни и те же модули и системы
можно встретить на машинах разных марок и классов. Унификация позволяет
выходить на рентабельный объем производства отдельных узлов даже при
достаточно скромном выпуске конкретных моделей.
Увы, у нас в стране процесс унификации автокомпонентов до сих пор только
обсуждается. Первые контакты были установлены между АВТОВАЗом и «Иж-Авто»;
ряд наработок был у вазовских инженеров с коллегами из Нижнего Новгорода.
Перспективные модели, за которыми будущее российского автопрома, непременно
будут унифицированы, но вероятнее всего не друг с другом, а с… иностранными
моделями.
ТОЛЬКО В СРОК!
Усилившаяся в последнее время конкуренция заставляет российские автозаводы
поднимать планку требований в области качества – и в первую очередь к своим
поставщикам. При этом, как правило, заказчик ставит условие: повысить
качество, не повышая цену! А то грозятся найти альтернативу. Кроме того,
сейчас практически на всех российских автозаводах внедряется система
«бережливого производства», которая предполагает снижение товарных запасов и,
соответственно, вводит требование к поставщикам осуществлять поставки точно в
срок (Just in time).
Так что времена, когда автозаводы вынуждены были брать любые комплектующие на
любых условиях – других-то все равно не найти! – остались в прошлом.
Навсегда. И выживут только те производители компонентов, кто сможет играть по
новым правилам.
НАША СПРАВКА
В России уже работают СП с известными компаниями: Robert Bosch (выпуск
элементов систем зажигания, светотехники), Siemens VDO (электронные
автокомпоненты), Tenneco Automotive (детали выхлопных систем), Jonson
Controls (сиденья), Magneti Marelli (светотехника), Delphi (автомобильные
электрожгуты), ZF (производство коробок передач для тяжелой спецтехники),
Cummins (двигатели для грузовиков), Federal Mogul (детали тормозных систем и
сцепления).
Сейчас на российском рынке автокомпонентов работает около двух тысяч
компаний разного масштаба; через 5–7 лет останется только 1200–1300.
Источник информации
За рулем №11 2007
|
Главы из
монографии Губкин С.И. «ПЛАСТИЧЕСКАЯ ДЕФОРМАЦИЯ МЕТАЛЛОВ»
ГЛАВА 1. Часть 4. Упрочнение (Наклеп)
Интенсивность увеличения сопротивления деформированию с увеличением
степени деформации отображает эффект наклепа. Интенсивность наклепа зависит
от особенностей пластического процесса при данных условиях деформации…
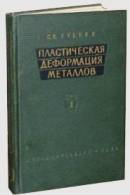
подробнее
>>
Губкин
С.И. Пластическая деформация металлов. Том II. Физико-химическая теория пластичности. - М.:
Металлургиздат, 1961. – 416 с.
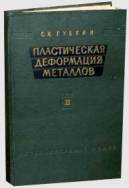
подробнее
>>
Губкин
С.И. Пластическая деформация металлов. Том III. Теория пластической обработки металлов. - М.:
Металлургиздат, 1961. – 306 с.
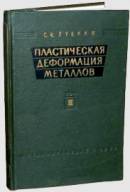
подробнее
>>
Ковка и
штамповка: Справочник. В 4-х т./Ред. совет: Е.И. Семенов (пред.) и др. – М.:
Машиностроение, 1985 – т. 1. Материалы и нагрев. Оборудование. Ковка / Под
ред. Е.И. Семенова. 1985. – 568 с.: ил.
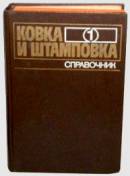
Содержание
книги >>
Ковка и
штамповка: Справочник. В 4-х т./Ред. совет: Е.И. Семенов (пред.) и др. – М.:
Машиностроение, 1986 – т. 2. Горячая штамповка / Под ред. Е.И. Семенова.
1986. – 592 с.: ил.
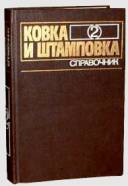
подробнее
>>
Ковка и
штамповка: Справочник. В 4-х т./Ред. совет: Е.И. Семенов (пред.) и др. – М.: Машиностроение,
1987 – т. 3. Холодная объемная штамповка / Под ред. Г.А. Навроцкого. 1987. –
384 с.: ил.
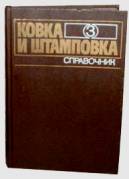
Содержание
книги >>
Ковка и
штамповка: Справочник. В 4-х т./Ред. совет: Е.И. Семенов (пред.) и др. – М.:
Машиностроение, 1985 - 1987 – т. 4. Листовая штамповка / Под ред. А.Д.
Матвеева. 1985 - 1987. – 544 с.: ил.
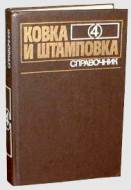
подробнее
>>
|